5 Ways Asset Life Cycle Management Produces Better Outcomes
Most engineering companies don’t consider the maintenance and operation costs of an asset during the design and initial capital engineering phase of the project. They’re fixated on reducing the initial cost of the asset while still ensuring the asset is ready for operation as scheduled.
While cost cutting is appealing in the short term, long-term project planning offers an integrated approach that provides a realistic overview of the cost of an asset over its lifespan.
Asset Life Cycle Management
An asset’s life cycle encompasses every stage of an asset from the decision-making process to the asset’s decommissioning. Typically, the life cycle of an asset is split between the capital project planning side and the operations side, with the handoff from capital to operations occurring after the asset’s installation.
Whether you are designing a new plant, revamping a brownfield site, or replacing a single piece of equipment, Asset Life Cycle Management brings the foundational knowledge of operational and maintenance management to the initial design phase, closing the gap and combining capital engineering with maintenance, reliability, and manufacturing operations. It considers the lifetime cost of operating an asset and creates a long-term comprehensive solution for asset-owning companies.
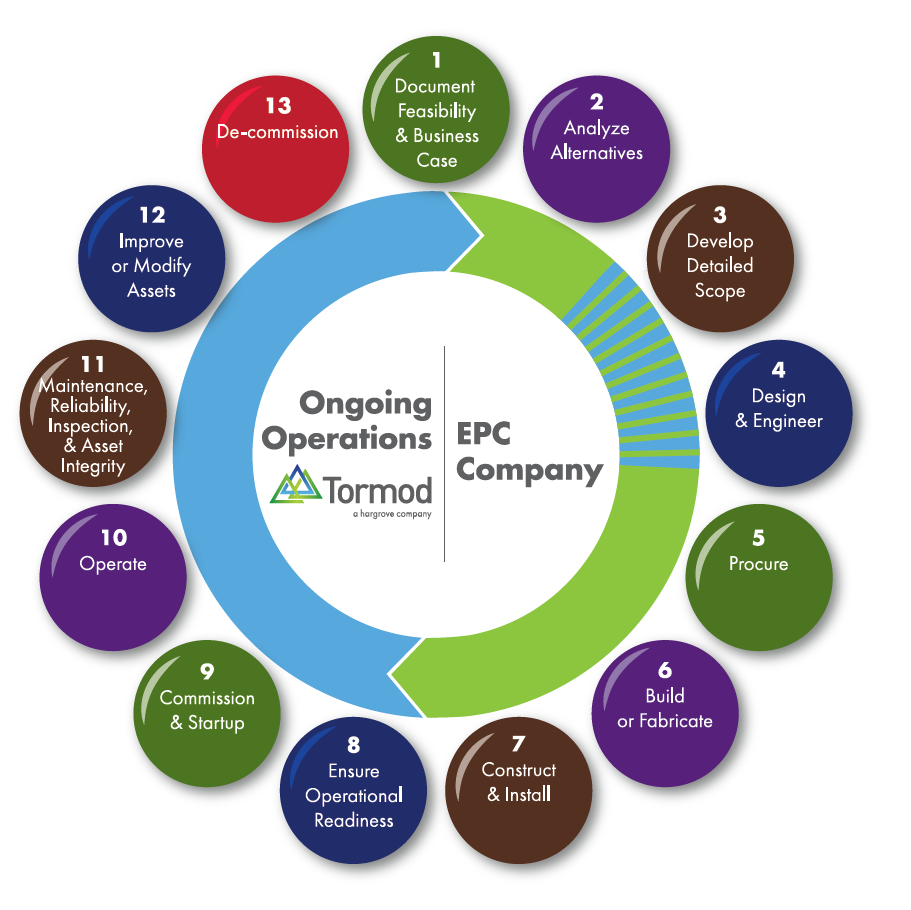
Benefits of Asset Life Cycle Management
Inheriting a project you’ve already paid for that isn’t meeting expectations is detrimental to your budget. Overall, front-end planning is the low-cost and optimal solution. Approaching capital projects using Asset Life Cycle Management provides substantial cost savings and offers your company a strategic, sustainable advantage.
1) Alignment of Stakeholders
Your capital project team typically works with an asset only until the asset is installed and ready for operation. However, your maintenance and operations managers will live with the asset for 20-50+ years until decommissioning.
Implementing Asset Life Cycle Management brings together stakeholders from all sides of the table to make decisions regarding asset reliability and maintainability. With all stakeholders involved—site managers to chief executive officers—budgets will be created based on decisions that serve long-term needs. How an asset will be constructed, operated, installed, and maintained must be built into the design.
In addition, decisions on spending will occur with the input of all stakeholders. There’s always a choice on where to invest money. Do you pay an employee to manually collect data, or do you invest in Industry 4.0? If you invest in new technology, will you hire new talent who has the requisite knowledge to use it? Or will you train your current team? Will this implementation require a redesign of equipment? The way in which you make gradual changes is often what provides real value to your organization.
2) Key Performance Indicators projected during Design Phase
Key performance indicators (KPIs) during the engineering phase of a project are focused on safety and scheduling. How well did you adhere to the agreed-upon terms? Your capital project engineering manager needs to know if the asset was installed on budget and schedule and if the asset was installed safely. However, your maintenance and operations managers want to know how well the asset is running.
Asset Life Cycle Management focuses on bringing a high level of operational and maintenance knowledge through the life cycle of the asset. With your operations and maintenance groups involved in the design phase, KPIs based on the performance, profitability, and quality of the asset are engineered into its design. This focus will not add overall cost to your project but will greatly decrease the total cost of ownership throughout the asset’s life cycle.
3) Sustained Return on Investment
By looking beyond capital engineering, asset-owning managers are able to make the right decisions at the capital project planning phase regarding the long-term operational impacts of the asset. The advantage of considering operability and maintenance in the detailed design phase results in long-term savings that reduce the number of unexpected problems related to your asset.
If maintenance processes and procedures were correctly analyzed and written during the initial phase, your project will incur less late changes, less prolonged outages, reduced downtime related to failures, less maintenance overtime, reduced energy costs, reduced raw material waste, and potentially a reduction in the cost of required spare parts.
4) Designed for Reliability and Maintainability
Most companies don’t truly design for a defined life expectancy. The result is a higher life cycle cost of ownership due to over-design or under-design that results in reliability failures and their resultant costs.
Asset Life Cycle Management ensures that the asset design supports the turnaround frequency and the required productivity of the asset. This means your asset will be operating safely, efficiently, and profitably until the next scheduled downtime.
5) Embedded Sustainability
The selection of materials and equipment — elements that alter one’s carbon footprint — usually can’t be implemented after an asset’s installation. Engineering sustainability into your project should be completed early in the capital process phase so the asset is designed to achieve your sustainability goals. If you don’t design-in sustainability improvements, it may be impossible or extremely costly to modify-in later.
The United Nations outlined 17 sustainable development goals as part of their Global Sustainability Compact. Whether your specific sustainability initiatives involve energy, climate change, or clean water, it’s most impactful to design with sustainability in mind.
Teaming with Industry Specialists
Asset Life Cycle Management gives an all-encompassing approach to the long-term stewardship of an asset from planning and design to operation and maintenance.
Many companies struggle with the in-house experience to implement Asset Life Cycle Management because of generational retirement and a lack of available skilled workers. Many companies are also realizing that their operating and maintenance procedures are outdated, further complicating the impact of retirements. As the workforce evolves, asset-owning managers are looking to industry specialists to fill the knowledge gaps and facilitate discussions.
Tormod offers differentiated solutions with the asset’s entire lifespan in mind, customizing your project with reliability, sustainability, and maintainability built into the design to achieve business and financial objectives.
To implement Asset Life Cycle Management for your next project, contact us.